在化工、半导体、医疗等高精度制造领域,透明聚四氟乙烯管(PTFE)凭借其优异的耐腐蚀性、低摩擦系数和透明特性,成为流体传输系统的核心部件。然而,其低导热性、高弹性模量等特性导致切割过程中易出现毛刺、变形或尺寸偏差,直接影响密封性能与使用安全。
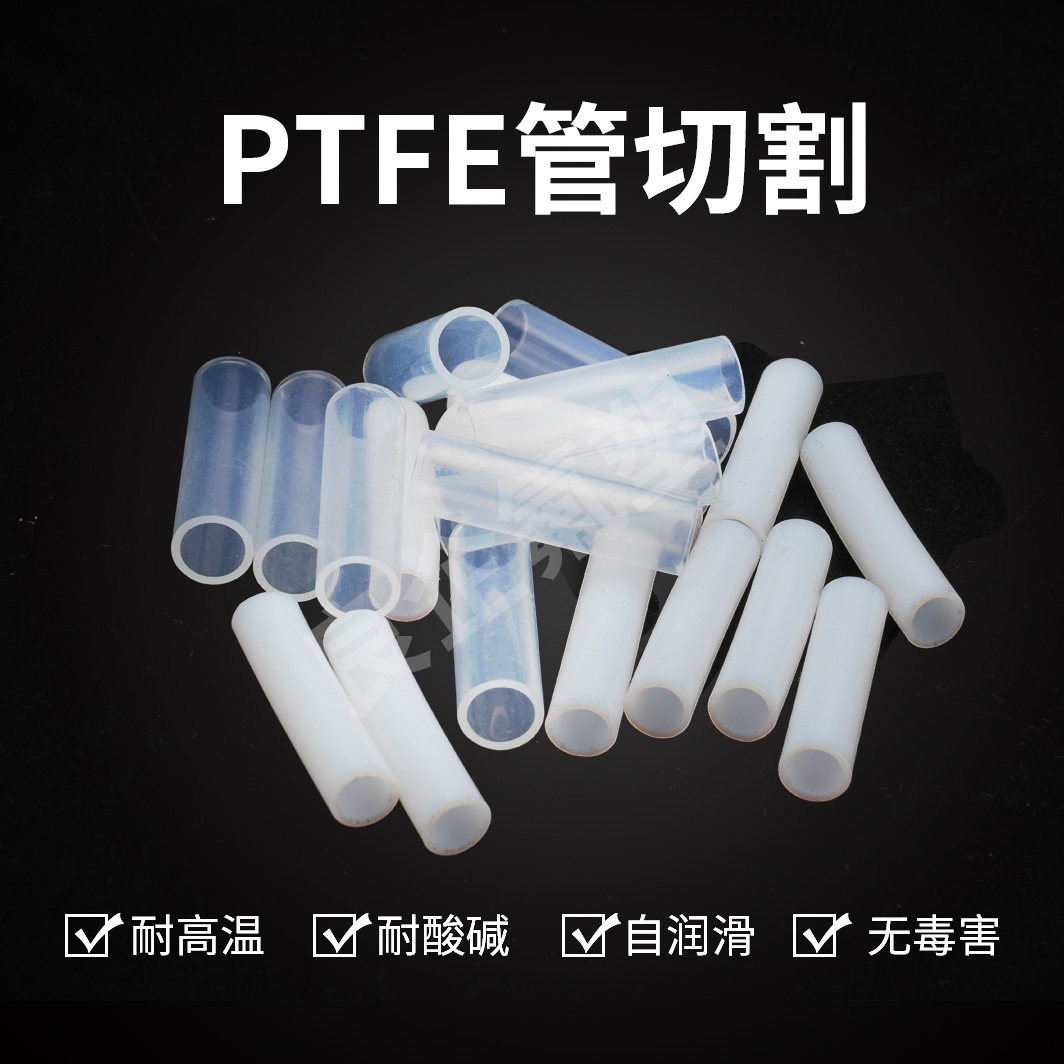
一、材料特性对切割工艺的挑战
透明聚四氟乙烯管的物理特性决定了其切割难度:
低导热性:切削热难以传导,易导致局部软化变形。
高弹性模量:切割时易产生弹性恢复,造成尺寸误差。
化学惰性:传统冷却液可能污染材料,需采用专用润滑方案。
某半导体企业实测数据显示,传统切割工艺下,透明PTFE管的切口平整度偏差可达±0.2mm,而高精度应用要求控制在±0.05mm以内。
二、核心工艺参数优化指南
1. 刀具选择与参数配置
刀具材质:推荐使用金刚石涂层刀具,其硬度(HV9000)远超PTFE(HV20-30),可显著降低磨损。
几何参数:前角:20°-30°,减少切削力;
后角:15°-25°,避免后刀面摩擦;
刃口半径:≤0.1mm,降低切削阻力。
切削用量:切削速度:300-500m/min(较金属降低40%);
进给量:0.05-0.1mm/r;
切削深度:0.1-0.3mm(粗加工≤0.5mm)。
2. 冷却与润滑方案
干式切割:适用于薄壁管(壁厚≤2mm),通过高压气流(0.6-0.8MPa)实时吹除切屑。
微量润滑(MQL):采用植物基润滑油,用量控制在5-15ml/h,减少材料吸附。
低温冷却:液氮喷射(-196℃)可使材料脆化,降低切削力30%以上,但需控制冷却时间以避免热应力开裂。
3. 夹持与定位技术
自适应夹持器:三爪气动夹具,夹持力动态调节(50-200N),避免管材变形。
激光测距定位:精度±0.01mm,实现批量切割的尺寸一致性。
振动抑制:采用磁流变液阻尼器,将切割振动幅度降低至5μm以内。
三、先进切割设备与工艺
1. 双刀同步切割系统
某专利设备采用双椭圆切刀结构,两刀呈90°夹角布置,通过弹簧预紧力(50N)实现均匀切割。实测数据显示,该系统可使管材切口倾斜角≤0.5°,较单刀切割效率提升60%。
2. 激光切割工艺
波长选择:CO₂激光(10.6μm)对PTFE吸收率高,切割速度可达8m/min。
焦点控制:动态聚焦技术使光斑直径稳定在0.1mm,切口热影响区≤0.2mm。
辅助气体:氮气(纯度≥99.999%)吹扫,避免氧化发黄。
3. 水刀切割技术
压力参数:300-400MPa超高压水,混合石榴石磨料(粒度80目)。
切割路径:螺旋渐进式进给,减少水流冲击变形。
精度控制:通过闭环反馈系统,实时补偿水流扩散效应,尺寸精度可达±0.03mm。
四、质量检测与后处理
视觉检测:采用工业相机(分辨率5μm)检测切口毛刺高度,不合格品自动标记。
热处理去应力:180℃保温2小时,消除切割残余应力,降低后期开裂风险。
表面改性:等离子体处理(功率100W,时间30s)可提高管材表面润湿性,便于后续粘接。
五、行业应用案例
半导体设备:某晶圆厂采用激光切割+MQL工艺,将气体输送管路的颗粒污染等级从ISO Class 6降至Class 4。
医疗导管:通过水刀切割+等离子处理,实现导管端头0.1mm倒角,穿刺力降低40%。
化工管道:双刀同步切割系统使大口径PTFE管(DN100)的切口平行度偏差从±0.5mm降至±0.1mm。